MetaSense: Integrating Sensing Capabilities into Mechanical Metamaterial
Jun Gong*, Olivia Seow*, Cedric Honnet*, Jack Forman, Stefanie Mueller (* co-primary authors) ACM Symposium on User Interface Software and Technology (UIST), 2021 [PDF] [Video]
Motivation
While early work in personal fabrication focused on designing the outside of objects, recently researchers proposed to also consider the internal structure of objects as an important design element. By dividing the inside of objects into grids of repetitive cells and modifying the parameters of the cells, researchers were able to achieve various mechanical properties. These so called mechanical metamaterials can make objects harder or softer and more or less flexible through their specific internal geometries without changing the outer geometry or printing material. To push this idea further, Ion et. al. proposed metamaterial mechanisms, which are cell structures that transmit input forces in one location to output forces in another when cells are being deformed.
To augment such mechanical metamaterial structures with sensing capabilities, researchers investigated how to integrate different types of sensing elements. For instance, Helou et al. and Nick et al. showed how to embed discrete digital switches and logic gates into mechanical metamaterials. However, while these works are able to sense discrete states when the metamaterial structure is being deformed, they are not able to continuously sense deformation. In addition, the sensing elements are created by either manually filling liquid metal channels inside the metamaterial or by applying conductive ink to the passive metamaterial structure. Furthermore, placing the sensing elements inside the metamaterial structure requires expertise and no support tool was provided by these prior works to help users with quickly prototyping metamaterial structures with various sensing capabilities.
In this paper, we explore how to go beyond sensing discrete states by developing an approach to add continuous deformation sensing to mechanical metamaterials. Inspired by work on conductive shear cells as sensors, we propose to integrate these cells into mechanical metamaterial devices. Each conductive shear cell contains two opposing conductive walls. When a user is manipulating the metamaterial device, the distance and overlap area between the two opposing conductive walls of a cell change accordingly, resulting in a capacitance variance that can be measured. This is depicted in the figure below.
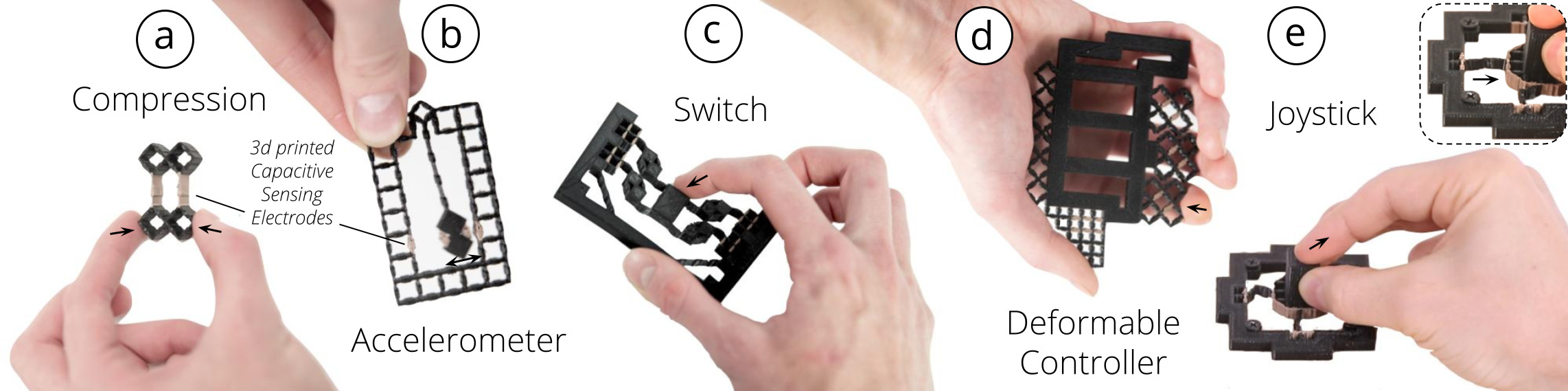
To help designers create mechanical metamaterial devices with continuous deformation sensing, we built a 3D editor that computes the optimal locations for placing conductive shear cells within the structure. We accomplish this by running a mechanical simulation which identifies the cell walls with the greatest deformation and thus the greatest capacitance variation, which are ideal candidate locations for sensing cells. On export, the editor creates two .stl files for multi-material 3D printing with conductive and non-conductive filament, eliminating the need for manual assembly. After 3D printing, users only have to connect the conductive cell walls to our sensing hardware and the interactive object is ready be to be used. To evaluate the effectiveness of our approach, we tested conductive shear cells of varying sizes and found that even small cell sizes (5mm x 5mm) support robust capacitive sensing.
In summary, our primary contributions are: (1) the development of metamaterial devices with continuous deformation sensing enabled by measuring capacitance variation caused by the deformation of conductive shear cells, (2) a design and fabrication pipeline based on multi-material 3D printing that supports designers in placing conductive shear cells in optimal sensing locations based on a simulation of mechanical deformation, (3) a study to validate the feasibility of our sensing approach with different cell parameters (e.g., thickness, width); and (4) a series of applications to showcase the sensing capabilities and interactions enabled by our technique.
For more details, please refer to the project page hosted in MIT HCIE and MIT Media Lab.
Selected Press Coverage
MIT News: Engineers create 3D-printed objects that sense how a user is interacting with them
Hackster.io: MetaSense Integrates Sensing Capabilities Into Mechanical 3D-Printed Parts